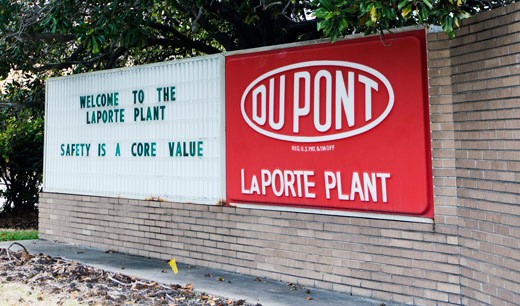
HOUSTON – This month marks the 30th anniversary of history’s worst industrial accident. Thousands of people were killed by leaking methyl isocyanate at a Union Carbide plant (later bought by Dow Chemical) in Bhopal, India. The U.S. Chemical Safety Board (CSB), an independent federal agency charged with investigating chemical accidents, has a video commemorating the event on their website. The CSB stated in the video that 3,800 people were killed in the catastrophic incident and according to the Indian government, resulted in over half a million serious and disabling injuries. According to Indian government estimates, lingering effects of the hazardous chemical release pushed the death toll to about 15,000 over the next few years. The CSB discusses how much more must be done to prevent similar accidents from occurring.
What is the current status of personal and process safety in the chemical industry? Recent events in Texas paint a discouraging picture.
In November, four workers died and one was injured at a chemical plant in La Porte, Texas after the release of a hazardous chemical. The Harris County Medical Examiner reported that two brothers, Robert and Gilbert Tisnado, died in the incident, along with Wade Baker and Crystle Wise.
The incident occurred at the Sabine River Works DuPont La Porte Plant on Nov. 15 at 4 a.m., when methyl mercaptan, a highly regulated hazardous chemical, was released from a failed valve inside an operations building. The gas release went past the fence line into adjacent communities and residents complained about the smell. The smell was reported in towns several miles away from the plant. As usually happens in these incidents, emergency response actions were inadequate.
Houston’s ABC 13 News reported that “emergency management officials say that it’s already clear that the response to the leak was inadequate and slow, especially given the scope of the disaster. The site had been plagued with recurring maintenance problems, and workers lacked adequate access to breathing equipment that would have given them a better chance to survive.”
Despite its common use, this chemical has the highest National Fire Protection Association (NFPA) hazard rating of 4 for health and fire. The Occupational Safety and Health Administration (OSHA) sets a personnel exposure limit of 0.5 ppm (parts per million) time weighted average and NIOSH (National Institute for Occupational Safety and Health) recommends a ceiling of 0.5 ppm for maximum of 15 minutes. Short term exposure can cause coma or suffocation from asphyxiation. Methyl mercaptan has an LC50 rating of 675 ppm, meaning that it is lethal to 50 percent of rats at a concentration of 675 ppm. The chemical was stored as a liquid but quickly becomes a gas upon release. The DuPont incident site stores as much as 250 tons of methyl mercaptan. The stored quantity of this extremely hazardous material could have posed a more serious problem to the workers at the site and the community.
The New York Times reports that another chemical produced at the facility is methyl isocyanate, the same chemical released at the Bhopal site that killed thousands of people in 1984. Methyl isocyanate was not involved, this time, in the hazardous release incident.
OSHA and the U. S. Chemical Safety Board launched an investigation into the incident.
What’s the matter with DuPont?
DuPont is recognized as a leader in the chemical industry when it comes to industrial safety. When fatalities occur in such a highly regarded company, questions arise about the current state of process safety. Process safety is a blend of engineering and management skills focused on preventing catastrophic accidents, particularly explosions, fires and toxic releases associated with the use of chemicals and petroleum products.
DuPont is not a small or inexperienced company. DuPont was founded in 1802 as a gunpowder mill by E. I. du Pont and later on went on to manufacturer dynamite. DuPont is a multinational corporation and one of the largest chemical companies in the world. At one time, DuPont, through Christiana Securities, was the major stockholder with controlling interest in General Motors. This controlling interest allowed it to monopolize GM’s paint and fabric business.
The U. S. Chemical Safety Board has previously investigated four accidents at DuPont facilities; a 2010 phosgene release at the DuPont Plant in Belle West Virginia resulting in one fatality and that same year a hot work accident at the DuPont facility outside of Buffalo, NY, fatally injured one worker. The plant had previously been cited by the Environmental Protection Agency for environmental violations.
Texas continues to experience a large number of fatalities, chemical releases, fires and explosions. EHS Today reports that nearly 5,000 workers die each year as a result of fatal occupational injuries in Texas. These preventable deaths devastate families and workplaces.
The incident in La Porte is the latest in a deadly string of incidents in the petrochemical hub of Texas’s coast region and is the worst such loss of life in an industrial accident since 2005. That year, a British Petroleum (BP) refinery explosion killed 15 workers in Texas City. The Texas City Refinery is the third largest refinery in the U.S. and is located at the world’s biggest petrochemical complex. An investigation by People’s World, after the 2005 explosion, confirmed that safety procedures and practices had deteriorated after OSHA and the U.S. Chemical Board inspectors left the refinery and after the facility was sold by British Petroleum to Marathon Oil.
In April 2005, OSHA cited the BP Texas City refinery and listed the BP Texas City refinery as a subject facility under its Enhanced Enforcement Program for Employers Who Are Indifferent to Their Obligations Under the OSH Act.
On the same incident, the U.S. Chemical Safety Board stated in their recommendations: “The Board believes that the foregoing circumstances and preliminary findings raise serious concerns about (a) the effectiveness of the safety management system at the BP Texas City refinery; (b) the effectiveness of BP North America’s corporate safety oversight of its refining facilities; (c) a corporate safety culture that may have tolerated serious and longstanding deviations from good safety practice
Poor safety – Texas style
According to a recent Dallas Morning News investigative report, “Houston has the worst record in Texas and Texas has the worst record in the nation when it comes to workplace fatalities or catastrophes.”
Texas is but one of 25 states that have no safety inspection agency. The state omission further burdens OSHA, impacted like many federal agencies, by repeated governmental shutdowns and cutbacks. The results in this shortfall can be seen in the 2013 ammonium nitrate explosion at a fertilizer plant in West Texas that killed 15, injured 150 and destroyed part of the town. The West Fertilizer plant in West Texas had not been inspected in 28 years. Ammonium nitrate was the chemical explosive used by right-wing extremist to demolish the federal building in Oklahoma City.
In response to this incident, President Obama issued Executive Order 13650 on August 1, 2013, directing federal agencies to modernize and improve chemical facility safety.
Other notable industrial incidents in the Houston ship channel area include 23 fatalities and 130 injuries at a Phillips Petroleum explosion in 1989 in Pasadena TX. In 1990, 17 died and 5 were hurt at the Atlantic Richfield chemical plant near the Houston Ship channel.
Fatal industrial incidents will continue to occur unless occupational and process safety regulations are made more effective. Despite recurring incidents, corporations and Republican and some Democratic Party elected officials continue to call for less regulation and resources.
“Let free enterprise reign, and be wary of overregulation,” Texas Governor Perry declared in a 2009 speech at the Central Texas Construction Expo. “All that regulation adds to your overhead and you can’t operate at a profit.”
Safety does not equal profits
OSHA does not have the resources to effectively enforce its current process safety regulations. The U.S. Chemical Safety Board only issues recommendations because it lacks citation and fines authority. Because corporate management is not criminally charged for failure to comply with safety regulations, there is little incentive to slow their drive for added profits, while increasing process safety risk. Corporations like DuPont and BP are increasing profits by cutting personnel, cutting operating budgets, cutting maintenance costs, cutting design costs, outsourcing work and lobbying for less government regulation. Corporate management mandates cost cutting and fails to take responsibility for the negative process safety impact. Corporate management budget pressures force lower level management to take on additional risks.
Process safety begins with enforcement of generally accepted good engineering practices in the design, training, operation, maintenance and inspection of process equipment. The OSHA Process Safety Management of Highly Hazardous Chemicals program is performance based. Recent hazardous chemical releases and explosions have demonstrated that the industry’s process safety performance is lacking. Many federal investigations have pointed out systemic deficiencies. While the DuPont investigation will likely point to individual plant workers failure to follow some written procedure, high level management decisions will probably not receive the same level of scrutiny. Good safety investigations use root cause failure analysis to arrive at system causes and solutions. Workers get killed when systems fail and these failures start with corporate management. Some necessary steps must include federal legislation and/or Presidential Executive orders to empower workers and worker committees to shut down unsafe operations and mandate frequent federal inspections of each site, with fines assessed according to corporate profits gained from cost cutting and deferred remediation. One practical and immediate response is to install and monitor hazardous chemical sensors just outside petrochemical facilities to ensure exposure compliance and assist in a rapid response program for residents near the facilities.
An intrinsic conflict of interest exists between private interests (corporate profits) and the public interest. Only a strong public involvement in the form of effective government regulations and strict enforcement will help to turn the tide on process safety and work related injuries. Given that lives are at stake, Americans should not wait for another Bhopal catastrophe to take more effective action to prevent industrial safety deaths and injuries.
Photo: This undated image shows signage at the DuPont Facility in La Porte, Texas. Four workers were killed and one was injured Nov. 15, during a hazardous chemical leak at the suburban Houston plant. (AP Photo/Houston Chronicle, Marie D. De Jesus)