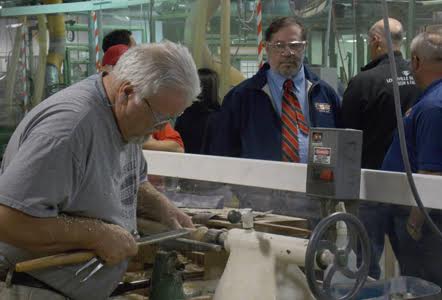
LOUISVILLE, Ky. (PAI) – For members of Steelworkers Local 1693 at the Louisville Slugger factory in Kentucky, every day is baseball season.
The 60 USW members there work for Hillerich & Bradsby (H&B), the family-owned company that has run the Slugger plant for 131 years. The H&B workers produce the iconic wooden bats prized by the most famous hitters in the history of the national pastime.
“We work hard, and we take pride in our bats,” USW member Terribo Kohn said as he applied brown stain to the barrels of a batch of souvenirs.
The factory, a block from the Ohio River in downtown Louisville, produces 4,000 unique types of wooden bats – from ash, maple and birch – for professional baseball games, as well as souvenir giveaways and retail sales. The workers produce, on average, 3,200 bats each day for souvenirs and retail sale and about 300 bats per day for major league baseball players.
Rhonda Kaninberg, who has worked at the factory for 12 years, said while H&B has about 40 competitors in bat-making, Slugger products stand apart from the rest. “There are other baseball bat companies of course, but not like this, not with this history,” Kaninberg said.
That’s because Louisville Sluggers have been in the hands of the game’s heaviest hitters, from Honus Wagner and Babe Ruth to Hank Aaron and Barry Bonds.
In addition to being the “official” bat of Major League Baseball (MLB), Louisville Slugger has contracts with individual major league players, including All-Stars such as Hanley Ramirez, Evan Longoria, Buster Posey, Joey Votto and Derek Jeter. The company creates bats to meet each player’s specific needs. In return, it can use the player’s signature on souvenir products.
While college basketball is the most popular sport for Louisville-area residents, baseball is king for the Slugger factory’s workers. Kaninberg, is a fan of the Reds – including Votto-in nearby Cincinnati but still feels “elated” when a player from any team scores a big hit using a Louisville Slugger. Added Kohn: “Working here makes you a baseball fan.”
Brittany Ray has worked at the Slugger factory for two years. One of her jobs is to create brands for custom bats by hand, using block letters to spell out the player and team names and bat model numbers and then to burn labels onto each bat, either directly onto the wood in the case of ash bats or with foil labels for maple and birch products.
A self-described “huge fan” of the now-retired Jeter, Ray said she took special delight in helping to produce bats for the former Yankees superstar to use in his final games.
But Louisville Slugger’s iconic status hasn’t protected H&B from financial worries.
Brian Hillerich, the company’s pro bat production manager, said declining sales and quality-control issues with non-wood products (made elsewhere) led H&B to sell the Slugger brand this spring to Wilson Sporting Goods Co. While Wilson will own the brand, H&B will continue to run the factory and will become Wilson’s exclusive supplier of wooden bats. The company also will continue to operate the adjacent museum and conduct tours of the factory, which receives 300,000 visitors each year. “It hurts to say it,” Hillerich said, “but for the brand, the sale is probably the best thing that could have happened.”
USW Unit President Glen Seabolt, who has worked at the Slugger plant since 2006, doesn’t expect the sale to change the work environment in Louisville, where he said the local maintains an excellent relationship with management. “The family has been good to us. We provide them with what they need,” Seabolt said. “It is going to stay that way. We’ve got to step up, but we’re going to make it.”
Gordon Nichols, president of the amalgamated USW local, said H&B announced the sale in March after about a year of rumors. Because Wilson is well known for its strong support of American manufacturing, he expects the sale to ultimately be good news for workers. “Nothing has changed for USW members,” Nichols said.
Kaninberg said having USW at her workplace made her feel safer, especially after the sale. “Wilson is a union company, too. I don’t see them taking it anywhere. We feel secure,” she said. But the sale has not been the only change at the H&B plant over the years.
As he inspected and placed black painted bats in plastic sleeves to prepare them for shipping, USW member George Green said a buyout offer in 2006 led to a wave of retirements that made the H&B work force significantly younger. Still, Green said, the staff remains a good mix of newer and more experienced workers.
And the bat-making process has changed as well. For 100 years, workers made Sluggers one at a time using hand-operated lathes, and each bat took 20 to 30 minutes to complete. Now, automatic lathes perform the same functions in about 30 seconds.
The shift to automatic lathes happened gradually over a period of about four years, from the late 1980s to the early 1990s, said Danny Luckett, a 45-year employee who is the last worker remaining with the skills to make a bat by hand. Known to his co-workers as “The Legend,” Luckett said a more automated system reduced stress on workers’ hands.
“I couldn’t do it all day anymore,” said Luckett, who joined the work force at the age of 22 and plans to retire in June.
Some parts of bat-making are much the same as they were in the late 19th century. Wood from timberlands in New York and Pennsylvania arrives at the 30,000 square-foot facility in bundles of “billets,” or large, rounded pieces of wood. The highest-quality billets are set aside for major league bats.
The billets are fed into automatic lathes with precise settings to produce exactly the right size and shape. From there, the nubs are cut off each end, and the bats are smoothed and sanded, stained or painted, branded and then buffed to a shine before they are bagged and shipped. Through each step, a USW member handles each bat to ensure quality control.
“We still make the same thing, we just make it differently,” Luckett says. “We’re more efficient than we’ve ever been.”
Part of that efficiency is recycling the wood shaved off of billets during bat production. That sawdust travels out of the factory through an elaborate piping system and is eventually trucked to an Indiana farm for use as bedding in turkey coops. “Your Thanksgiving dinner probably slept on wood chips that came from a Louisville Slugger,” Hillerich joked.
Though the Major League Baseball season starts in March and runs through the end of October, the off-season – November through January – is the plant’s busiest time. Players and fans are getting ready for spring training and the start of the season. Business spikes again in September, as players prepare for the playoffs or for fall and winter developmental leagues.
While about half of all MLB players still use Slugger products and remain fiercely loyal to the brand, they can be very picky about their individual bats. “They handle them all day, every day,” said Hillerich. “If something is off by one-thousandth of an inch, they can tell.”
That attention to detail is part of what makes the dedicated USW work force in Louisville such an essential part of the success of the Slugger brand, Seabolt said. “We are the stewards of this brand, and we are proud of that,” he concluded.
Photo: Visit from International President Leo Gerard, USW Local 1693. Leo watching the most senior member Danny Luckett making a bat by hand. Luckett is the last member with this trade skill.